Steel Industry
Due to these challenges, steel plants face constant pressure to produce high-quality products in less time without any unexpected production halts. Unplanned downtimes can put the whole process on a stop, affect quality and production, and endanger the health and safety of workers on site. Online condition monitoring and predictive analysis is a value-added tool for the steel industry. It not only improves productivity in the plant but also makes operations more reliable and safer.
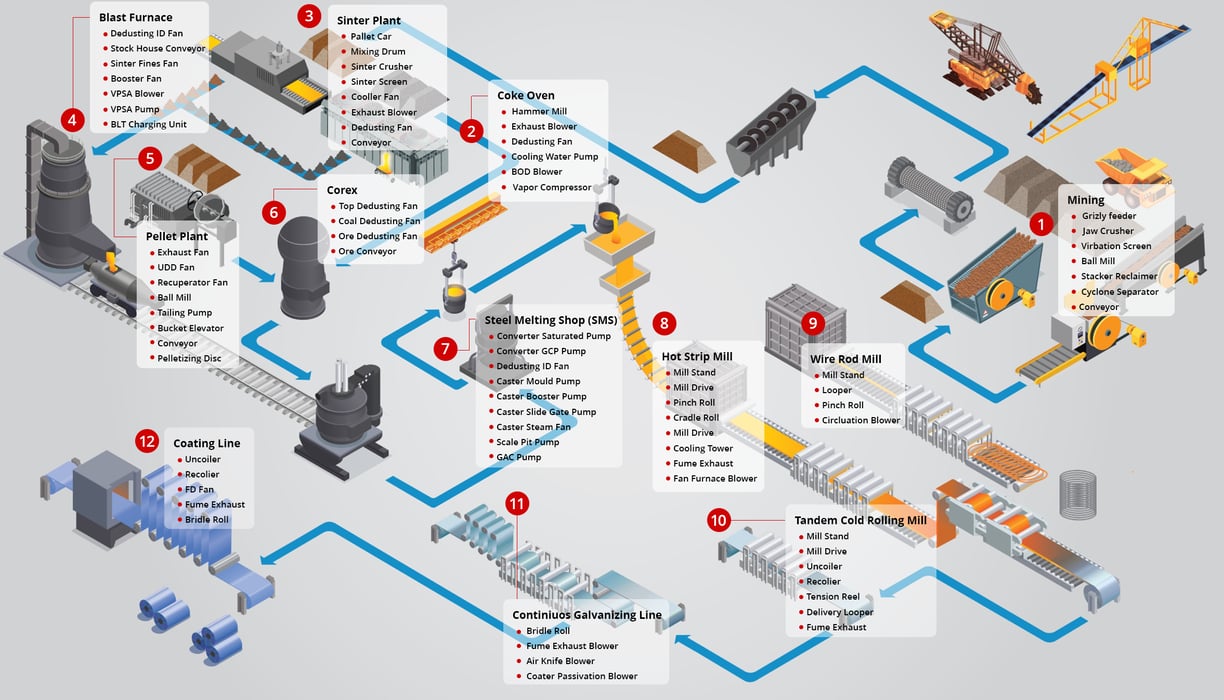
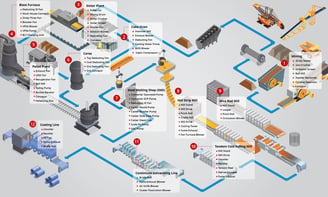
Steelmaking involves many manufacturing techniques which are time-consuming and complex. Apart from primary production processes, there are many sub-processes where the intermediate products are reheated, solidified, or pressed into various forms, like pipes, sheets, bars, rods, and different structural shapes based on the requirement. The primary steel manufacturing process is continuous and process-based, whereas the secondary manufacturing phases are discrete. What complicates it further is the fact that:
Production process parameters from the upstream steel manufacturing processes strongly influence the downstream ones.
The intermediate products in the process undergo both chemical and mechanical changes, making monitoring quality and output more difficult.
While steel manufacturing is already a complex process, steel plants may also face many on-ground challenges in maintaining efficiency, such as:
Older & legacy machinery
Frequent halts in production due to machine failure & downtime
Expensive coal & raw materials
Avoiding unexpected accidents on site
Various external factors like lockouts, strikes, inefficient administration, and shortage of raw materials